ボーイング777X型機の初号機中央翼が完成。 [2018年02月18日更新]

ニュース ピックアップ [ 最新情報 ]
スバルが遠隔操作型支援器技術を開発って、何のこと...
2025年08月12日 スバル
スバルショップ三河安城夏季休業のお知らせ。...
2025年08月09日 スバル
スバルがBEV第3弾を発表!その戦略を大分析。...
2025年08月09日 スバル
2025年ルマン総括。トヨタは如何にして破れたの...
2025年06月18日 スバル
間もなく、ルマン24時間!今年の優勝は誰だ?...
2025年06月13日 スバル
北米専売の2モデル、間もなくデビュー。...
2025年04月13日 スバル
ホンダ×日産=0。自動車産業が歩む、破滅必至の道...
2025年02月28日 スバル
ホンダ+日産=☓。画期的な提携交渉は破談に。...
2025年02月22日 スバル
次のページ>>1 2
スバルとSTI、2018年モータースポーツ活動計画を発表。
スバルは航空宇宙カンパニー半田工場にて、ボーイング777Xの初号機用中央翼の納入式典を開催しました。スバルは、現在半田工場にてボーイングの777と787、そして海上自衛隊向けの対潜哨戒機P-1用の中央翼ユニットを製造しています。
777Xは、ワイドボディの大型旅客機である777の発展型として開発中の機体であり、2020年の初就航を目指して開発が続いています。今回は、777Xが開発される周辺環境についてお伝えしましょう。
双発ワイドボディ機である777。
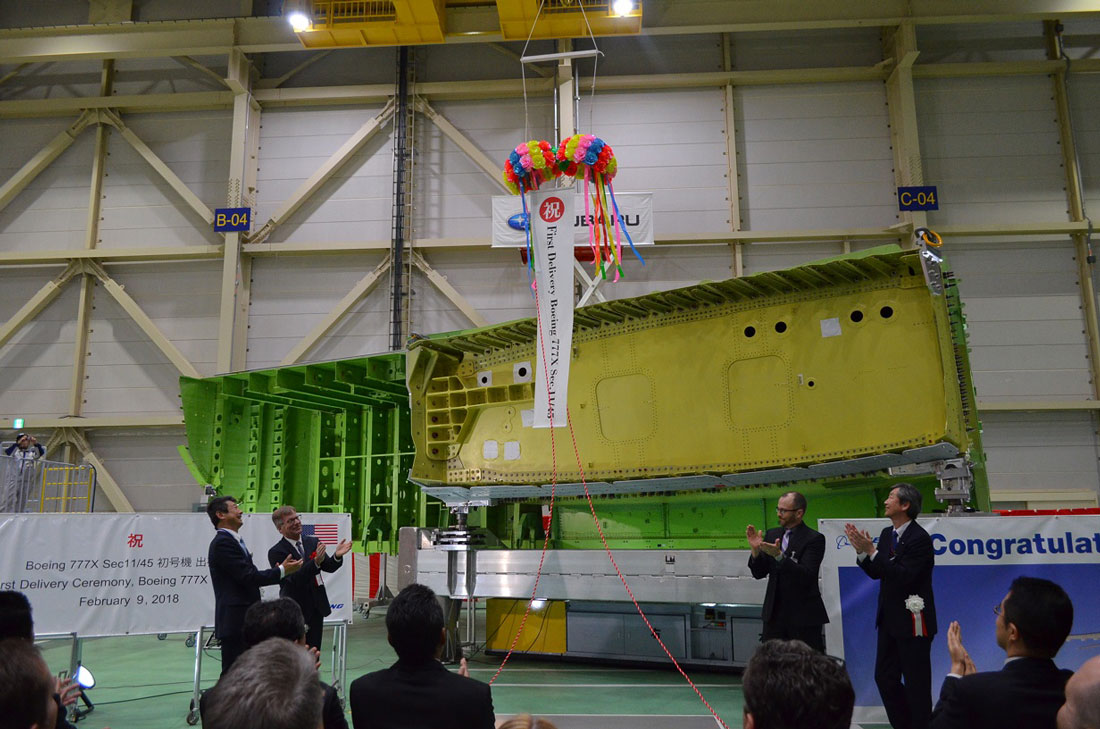
日本では、大型機と聞くとボーイング747「ジャンボジェット」を思い浮かべる方が多いと思います。数年前に、総2階建ての超大型機エアバスA380の就航も大きな話題となりました。ところが、現在の主流は超大型の4発機ではなく、777のような双発のワイドボディ機です。最新型747-8もA380も双方とも受注が不調のため、ライン閉鎖の危機に晒されているのが現状です。
ワイドボディ機とは、客室内に通路が2本ある機体を指します。これに対し、通路が1本のボーイング737やエアバスA320はナローボディ機と総称します。
双発機はエンジンが2発の機体であり、現在の旅客機の大半を占めています。777のような400席以上の大型機が双発となったのは、旅客需要の変化とジェットエンジン技術の進化が背景にあります。
60年前、航空機は高嶺の花でした。庶民は日数を掛けて船で大洋を渡り、一部の富豪のみが航空機を利用しました。それ故、航空券が高額なのは当然でした。ところが、近年では航空運賃の低価格化が急速に進行し、採算性も悪化。しかも、石油価格も高止まりの傾向にあります。その為、燃費に劣る4発機が急速に敬遠されるようになったのです。
賭けに勝ったボーイングと、負けたエアバス。
世界各地の航空需要が盛んになると、旅客需要も変化し始めます。ここで、ボーイングとエアバスの明暗が別れます。
今求められているのは、キメの細かい航空ダイヤです。例えば、超大型機が1日1便就航していたのを、中型機で1日3便にといった具合です。この方が、利用者が出発時間と到着時間を自由に選べるようになります。また、中型機であれば中規模都市へも直行便の運航が可能です。この考えに沿えば、超大型機よりも、燃費が良好で航続距離が長い双発の中型機の需要が伸びる、と予想されます。
一方で、主要都市の大規模空港をハブとして、ここからトランジットで中規模都市へ行くという形態もあります。もしハブ空港の利用が大勢となるのなら、超大型機で大量の旅客を一気に運ぶ方が良いはずです。その考えに沿うのなら、将来に渡って一定数の超大型機の需要が維持されると予想されます。
前者の需要予想に賭けたのがボーイングで、後者がエアバスでした。
ボーイングは747後継機を開発コストを節約した747-8で乗り切りつつ、中型機の787に全面注力。一方、エアバスは一気に勝負を賭けて、超大型機A380を就航させました。結果は、ボーイングの勝利。蓋を開けてみれば、747-8のオーダーは貨物機ばかり。A380は、話題こそ呼んだものの、就航には空港の改修が必須とあって需要が低迷。ライン閉鎖まで検討されているのが現状です。
兎にも角にも、燃料消費率と推力重量比の向上。
旅客機で重要なのは、1座席当たりの燃料消費量です。ある運賃を得るのに、どれだけの燃料費が掛かるか、という指標です。エンジンの効率が高いほど、利益率は高まります。つまり、旅客機用ジェットエンジンの良否は、推力重量比と燃料消費率で決まります。
推力重量比が良いというのは、軽量かつパワーもあるという事。一方、燃料消費率が低ければ、同じ燃料搭載量でより長距離飛行できますし、その分燃料搭載量を軽くして更に燃料消費を少なくもできます。
そこで、エンジンメーカー各社は熱効率工場と軽量化のため、技術開発を継続してきました。
ジェットエンジンの熱効率を決定づけるのは、兎にも角にも燃焼時の温度と圧力です。コンプレッサの効率向上により少ない段数で効率よく圧縮し、タービンの耐熱温度を向上させて燃焼温度を高め、エンジンコアの熱効率を向上させます。そして、その分より大きなファンを回転させて、大きな推力を獲得します。熱効率は向上し、燃料消費率は低下します。
ただ、2乗3乗の法則には注意せねばなりません。出力向上のためファンのサイズ(面積:2乗)を大きくすると、体積(=重量)は3乗で増加します。つまり、推力重量比がドンドン低下してしまうのです。
巨大なエンジンを抱える777が、今後も市場をリードする。
400席級の大型機を双発化できれば、多大なメリットが生まれます。メンテナンスコストは大幅に低減され、機体全体の推力重量比も改善されます。そうして実現したのが、ボーイング777です。エンジン直径は3m近くに達しており、地上滑走中には地面に擦りそうな程の巨大サイズです。
ライバルのエアバスA340が4発機ですから、777は大きな優位性をもって市場をリードしています。ボーイングは更に市場をリードする為に計画中なのが、発展型の777Xです。翼幅は6.5m拡幅され、全長も2m延長されます。その一方で、エンジンのファン直径は3.35mまで拡大され、出力は470kNまで強化されます。ただ、機体構造にはCFRPが多用され、8tもの軽量化が図られています。
計画中のバリエーションは、2タイプ。777-8は、短胴型で3クラス合計で350席。航続距離は17,200km。長胴型の777-9は最大425席で、航続距離は14,100km。777Xは、今後は設計の古いA340を尻目に市場を大きくリードしていくことでしょう。
世界最大の双発機777の開発。最大の課題は、「安全性と信頼性の証明」だった。
世界初の大型双発機である777の開発に際して、一番の問題が「安全性と信頼性の証明」でした。
片肺停止になると短時間しか飛行できない双発機には、長らく洋上運用に制限がありました。不時着陸に備えるため、島伝いの飛行ルートしか許可されなかったのです。
成田―ロサンゼルス間を直線で結ぶと、太平洋上に島がありません。ここに就航するには、アリューシャン列島沿いの北ルートか、南に迂回するグアム―ウェーク島―ハワイのルートしかありません。が、それでは双発機のメリットがありません。
今日、新型機開発の一番の関門は、FAA(米国連邦航空局)の耐空認証です。これが無くては、米国領土上では一切就航できません。米国市場を無視する訳にはいきませんから、FAAの耐空認証が実質的に航空機の安全証明となっています。
ボーイングは、777の機体及びエンジンの安全性と信頼性を証明することで、初めて長距離運行を可能にしたのです。
では、航空機の安全性と信頼性はどうやって「証明」するのでしょうか。
飛行中試験中の故障は人命に関わりますから、決して許されません。ですから、航空機は飛行する前、つまり「設計」こそ命。航空機における安全性と信頼性の証明とは「壊れないことの証明」ではなく、「設計の正しさの証明」なのです。
航空機開発に義務付けられた、2つの全機試験。
航空機の場合、FAAによって静強度試験と疲労試験の2種の全機試験が義務付けられています。2機の試験機は地上試験用に作られたもので、飛行に供されることはありません。静強度試験機はスクラップ、疲労試験機は展示用となるのが通例です。旅客機は実機試験の段階では既に売買契約が成立していますから、試験段階で深刻な異常が認められれば、キャンセルともなりかねません。
静強度試験は、主翼に荷重を負荷して、設計上の最大荷重時の異常の有無と、破壊荷重の値が設計上の値と合っているかを確認するものです。丸々1機の試験機を巨大な鉄骨の檻で囲い、飛行状態の荷重に近似するように何百という油圧シリンダーを接続していきます。
たった1回の決して失敗の許されない試験です。何千・何万という歪みゲージの値を記録しつつ、異常の有無を確認しながら、設計上の最大荷重まで慎重に荷重を増やしていきます。そして最後は、「ボキッ」といくまで、荷重を増やしていくのです。
設計より弱いのは当然不可ですが、設計以上に強い場合も、設計の信頼性が低いとして「不可」。静強度試験が完了すると、やっと試験機による飛行試験が許可されます。
静強度試験を横目に、疲労試験の準備が進められていきます。
同様に鉄骨の檻で囲われた疲労試験機にも、油圧シリンダーが接続されていきます。静強度試験と違って、主脚には着陸時の負荷を再現する油圧シリンダーを接続。上空での与圧の負荷を再現するため、胴体には加圧装置が接続されます。離陸滑走から離陸、上昇・下降、そして着陸。一連の飛行に伴う負荷を順番に負荷していきます。これを何千回と繰り返し、設計で想定した箇所が、想定したように、想定した回数まで耐えられることを確認します。
疲労試験には、かなり時間を要します。場合によっては、試験中に量産機の製造を開始し、発見された不具合は後で対策を施してから、カスタマーに引き渡すという場合もあります。
次のページ>>1 2
スバルショップ三河安城 店舗案内

>>最新情報一覧
