日本車の技術はなぜ停滞しているのか?その原因は何か? [2020年05月17日更新]
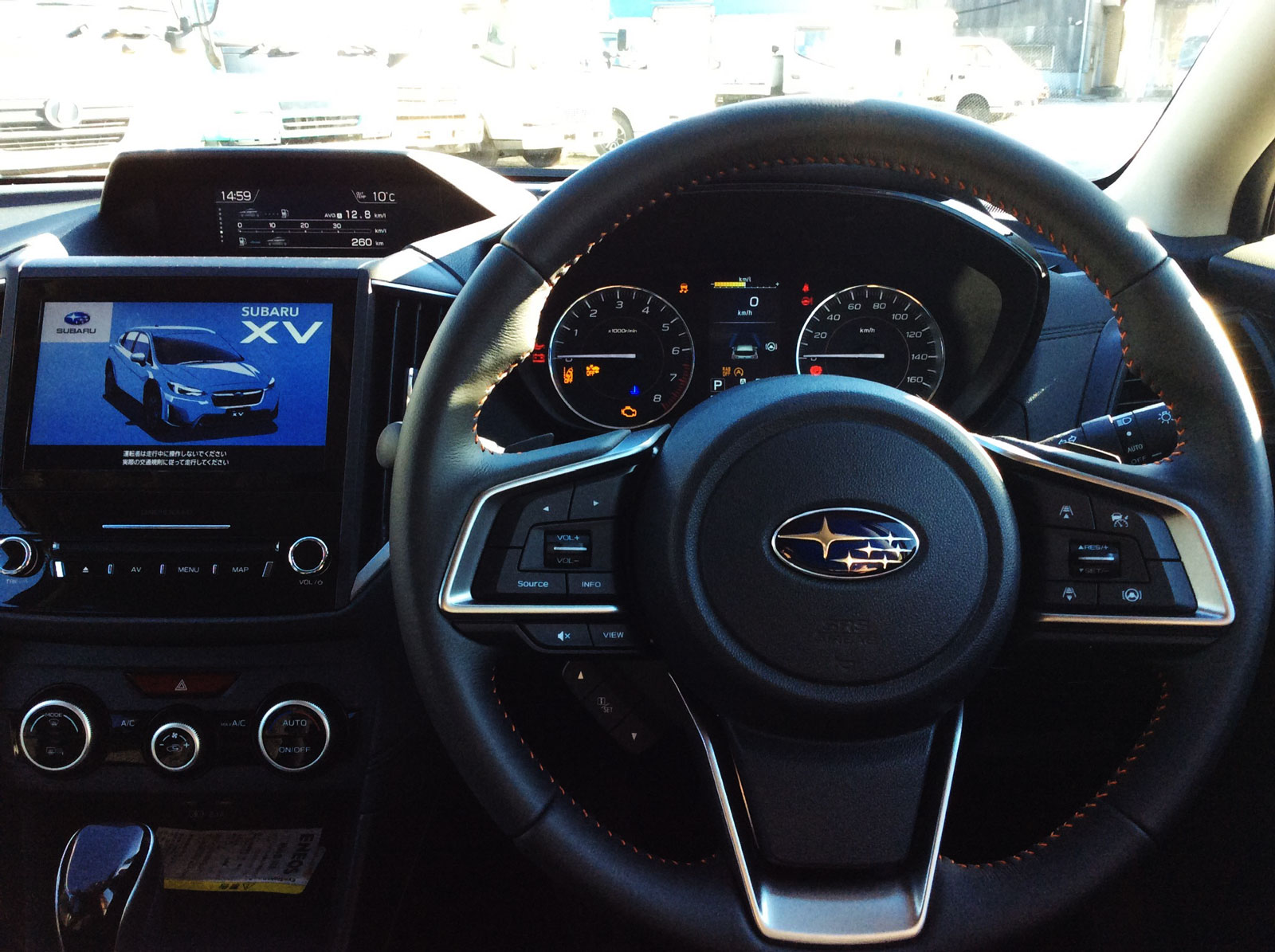
ニュース ピックアップ [ 最新情報 ]
スバルが遠隔操作型支援器技術を開発って、何のこと...
2025年08月12日 スバル
スバルショップ三河安城夏季休業のお知らせ。...
2025年08月09日 スバル
スバルがBEV第3弾を発表!その戦略を大分析。...
2025年08月09日 スバル
2025年ルマン総括。トヨタは如何にして破れたの...
2025年06月18日 スバル
間もなく、ルマン24時間!今年の優勝は誰だ?...
2025年06月13日 スバル
北米専売の2モデル、間もなくデビュー。...
2025年04月13日 スバル
ホンダ×日産=0。自動車産業が歩む、破滅必至の道...
2025年02月28日 スバル
ホンダ+日産=☓。画期的な提携交渉は破談に。...
2025年02月22日 スバル
次のページ>>1 2
日本車は、もう世界最先端ではない!?なぜ、先進性は失われたのか?
今、日本車は静かにピンチに陥りつつあります。欧州車に対する技術的格差が、ハッキリと広がりつつあるのです。
最も顕著に示すのが、メータパネル。今や、欧州車のメータパネルは、すっかりフル液晶が主流。鮮やかなビジュアルとモーションで、先進性を感じさせてくれます。漸く、トヨタ車で液晶化が始まったくらいで、日本車の多くは依然として「メータ盤+針」のまま。その差には、愕然とさせられます。
直近のMercedesのメータパネルは、先進性の象徴でしょう。ダッシュボードの上に、チョコンとタブレットのようなパネルがあるだけ。それ以外は、何もありません。殺風景ですが、先進性はハッキリと伝わってきます。
自動車は、やはりこうでなくてはいけません。「ナニコレ、新しい!」「こりゃ、スゴイな。」と、そう思ってもらわなければならないのです。愛用のマイカーの「古々しさ」を痛感させ、新しいクルマを魅力的に感じさせる。それが、代替えの動機になるのですから。
もちろん、こうしたインフォテイメントシステムは操作性に相当難があるため、一長一短があるのは確かです。しかし、世界に先駆けてデジタルメータを採用したのも、ナビゲーションシステムを採用したのも、ヘッドアップディスプレイを採用したのも、すべて日本車だったのです。このような領域で遅れを取ることは、日本車から大切な魅力の一つである「先進性」を奪う要因となっているのは、間違いありません。
フルモデルチェンジの度に重くなるのは、日本車だけ。
しかし、最も深刻なのは、メータパネルではありません。ボディ骨格の方です。LEXUS LS、Mercedes S、BMW 7、AUDI A8を比較してみて下さい。LEXUS LSだけが、200kgもの重量差があるのです。この差には、愕然とさせられます。
欧州車はこの20年、必死に軽量化に取り組んできました。鋼・アルミ複合構造や複合材料の導入。スポット溶接から、連続溶接+接着剤への転換等々です。その歩みは、困難の連続でした。VW・ゴルフなぞ、製造コストの問題から所定のモデルライフを早めてのフルモデルチェンジを2度も強いられています。それでも 未来の自動車あるべき姿を目指して一大技術革新へと邁進し続けてきたのです。
その間、日本車の骨格構造は「マイナーチェンジ」で足踏みしたまま、欧州車の進化をただ傍観してきました。高張力鋼板の採用は進んだものの、ハイエンドモデルでも昔ながらの鋼板製。漸く、構造用接着剤を導入が始まっていますが、依然スポット溶接が主役です。
スポット溶接は、鋼板を重ねて「点」溶接を行いますが、接合面積が少ないため、接合強度に劣ります。一方、連続溶接では突合せ溶接が可能なため、重ね代は不要な上に、接合面積が広いため、高い接合強度を誇ります。そのため、日本車はこれを見越して「頑丈」に強度設計を行わねばならず、その分重量が200kgも嵩むという訳です。
にも関わらず、頑なにスポット溶接を重用するのは、生産性のメリットがあるからです。スポット溶接は「速い」ですが、連続溶接は兎に角「遅い」のです。
欧州メーカーが多大な労苦と失敗の末に手に入れた、骨格構造の刷新。
骨格構造を一大転換するとなれば、生産設備はすべて刷新せねばなりません。すると、全鋼板製モデルとは混流生産が不可能となります。ところが、骨格構造を刷新するにしても、モデル毎にフルモデルチェンジのタイミングはバラバラですから、すべてのモデルが押しなべて刷新されるまでの間、凄まじい生産性の低下を招くことになるのです。そのため、日本の自動車メーカーは躊躇してきたのです。
加えて、鋼・アルミ複合構造は、従来構造とは全く異なる物理特性を持っています。アルミには降伏点はありませんし、固有振動数も異なります。互いを直接溶接することも不可能ですから、アルミや複合材料部分と鋼板部分の接合は、ボルト接合かFSW(摩擦攪拌接合)、構造用接着剤を用いるしかありません。
そこまで異なるとなれば、静的・動的剛性解析、衝突安全性能、NVH特性、生産性確保、原価低減、鈑金修理方法の確立、リサイクル、品質・性能保証等々。。。すべて基礎研究段階からやり直さねばなりません。総合的に考えて、この差は10年で早々に取り戻せる程甘いものではありません。
ここで最大の障壁となるのが、コストです。生産設備の新規導入、別途生産ラインの開設、生産コストの増大、開発コストの増大。。。1円1銭の積み重ねでコストダウンを進めてきた日本の自動車メーカーが、相当なアレルギー反応を示すだろうことは自ずと理解できるでしょう。
1990年代、日本が世界をリードした瞬間は確かにあった。しかし、今は。。。
バブル真っ盛りの1990年、ホンダは高根沢工場を新設します。この新工場、何と世界初のオールアルミモノコック構造である初代NSXのための専用工場。当時の日本車には世界一を目指す、凄まじい情熱と意欲が宿っていたのです。この当時の欧州メーカーの焦りは相当のものでした。初代セルシオやR32スカイラインGT-R等々、「安かろう悪かろう」と馬鹿にされてきた日本車が、欧州車を一部で凌駕し初めたからです。
1989年、日本車を叩きのめすため、あのメルセデスが禁断のシルバーアローの封印を解きます。あのメルセデスでさえ、日本車の脅威に怯えていたのです。このままでは、本当に追い抜かれるに違いないと。。。
ところが、近年の日本車には、当時の勢いはありません。「世界初」という言葉も殆ど聞かれなくなりました。なぜでしょうか?
それは、幹部級が極端にリスクを嫌っているからでしょうし、多くの若手が心底クルマ好きでないからでしょう。今や、自動車メーカーはクルマ好きのチャレンジの場ではなく、安定就職先の一つなのです。そうして就職した若手たちが、上司の反対を押し切ってまで、使命に燃えて邁進するでしょうか?「サー残」で会社に居残ってまで、自主的な研究会や勉強会を開くことがあるでしょうか?
80年代の日本車史に燦然と輝く金字塔の影には、そうした先人たちの努力が隠されています。だからこそ、世界をアっと驚かすことができたのです。もちろん、今だって夢と情熱を持った、優秀な若者は大勢居るはずです。しかし、硬直した上司と会社に失望し、優秀な若手ほど辞めていくと言います。
かつての日本の自動車メーカーは、[若手の気合と根性]+[上司の男気一発]で、難関を突破してきました。しかし、今はそういう訳にはいきません。長いものには巻かれろ、とは良く言ったものです。でも、意欲を失ってしまえば、「環境を変える」他ありません。つまり、転職です。。。
ものづくりは、人づくり。人を失っていくままであれば、日本の自動車産業に未来はありません。
硬直した組織体系が、若手のチャレンジングな意欲を削いでいく。
欧州のエンジニアには、終身雇用という考えは毛頭ないようです。彼らは、自分がエンジニアとして成長を遂げるために「優れた実績」を心底欲しています。機会ががあれば、どんどん手を上げて、意欲的に挑戦します。そして、そのチャレンジを通じて成長し、実績を(多少大げさに)履歴書に書き込んでは、自らの才を発揮できる環境を選んで次の企業へと移っていきます。
ただ、弊害も少なくありません。彼らの動機はすべて「自分のため」ですから、愛社精神のカケラもありませんし、ひと度経営が傾くと蜘蛛の子を散らすようにエンジニアたちは逃げていきます。部長級が部下を誘ってゴッソリ辞めるなんて事もあって、プロジェクトは中断を余儀なくされます。一番驚くのは、彼らが一切「引き継ぎ」をしないことです。メールの返信が無いので、バカンスかな?と思っていると、実はもう辞めていた、なんてのは日常茶飯事です。彼らには、立つ鳥跡を濁さずという言葉は無いようなのです。
日本では、最後まで責任を以て勤めることが、美徳とされてきました。転職するにしても、キッチリ引き継ぎを行います。それが、日本人の「当たり前」です。部下を誘ってゴッソリ辞めるなんてことは、「通念上」起こりにくいのかも知れません。
しかし、極端に人の入れ替わりが少ないがために、硬直した組織体系を生む遠因となっているのは、間違いありません。そして、そうした組織体系が、日本車から先進性と斬新さを失わせているのも確かです。
技術的困難を克服することこそ、日本車が最も得意とすることでした。驚くような先進技術を意欲的に投入し、世界をアッと言わせて来たのです。ハイブリッドだって、電気式4WDだって、PHVだって、FCVだって。みんな日本が先手を打った技術です。しかし、ここ数年、そんな勢いを感じることはスッカリなくなりました。特に、BEVの導入は、欧州・中国に完全に遅れを取ってしまっています。
あのモデルも、このモデルも、外注!?進む欧州メーカーの分業。
別の見方から、技術格差の要因を探ることもできます。日本と欧州の自動車産業では、分業制に違いがあります。欧州では、想像以上に分業が進んでいるのです。
殆どの方は信じないでしょうが、欧州メーカーのモデルのうち何割かは「外注業者の作品」です。例えば、コンパクトモデルのSUV版をラインナップしたいと望んだ時、欧州メーカーはコンペを開き、その勝者に丸ごと外注してしまいます。もちろん、プラットフォームや主力モデルは外注しません。しかし、派生モデルの多くは、実は外注なのです。
トヨタは、グループ会社のトヨタ車体に車両開発能力を付与し、国内向けミニバンをすべて「お任せ」にしています。もちろん、基本コンセプトやデザインはトヨタで行うのですが、車体開発や仕上げ等々はすべてトヨタ車体の仕事です。同じような事を、欧州メーカーでは完全なる「外部企業」に委託しているのです。
昨今のSUVブームによって、欧州メーカーはSUVのフルラインナップ化を図っています。日本より「こだわり度」が高い欧州メーカーが、これだけ大量のモデルをラインナップするとなれば、人員を大幅に増強せねばなりません。しかし、それでは経営上のリスクも増大してしまいます。だからこその「外注」なのです。
こうした企業としては、トヨタ・スープラの生産を手掛けるオーストリアのマグナ・シュタイアや、スペインの受託開発企業IDIADAなどが知られている他、エンジン分野では、イギリスのリカルドが知られています。また、少量生産のスポーツカーでは、モータスポーツ企業の躍進が目立ちます。イタリアのダラーラ、イギリスのコスワース、プロドライブの他、各F1チームもエンジニアリング会社を設立し受託開発業務を行っています。
欧州メーカーは、外注によって得られた「余力」を先進技術分野に振り向けることで、その先進性を維持しているのです。外注化は、選択と集中の一環なのです。
契約社会の欧州サプライヤーと、日本で取引する難しさ。
もちろん、外注にはリスクもあります。情報漏洩は特に深刻な問題ですし、品質や設計に関わる問題に関する責任の所在も厳密に規定しなければなりません。そのため、欧州ではたった1個の部品供給でさえ、分厚い契約書が必要です。所定の契約作業が済んだ後、互いの顧問弁護士が丁々発止をやり合いつつ緻密な契約書を作り上げていくのです。
ディーゼルゲート事件の際、ECUを受託製造するボッシュは、自らが無関係であることをいち早く公表しました。日本人的感覚からすれば、ちょっと冷たい?客先に文句を言って大丈夫?と思わずにはいられないやり方です。
でも、彼らからすれば、契約上OKならば、完全なるノープロブレム。それは、道義的な問題ではなく、すべて契約上の問題での話しなのです。自社の顧問弁護士が責任なし、と判断すれば、その立場で争っていく。それが、欧州のやり方なのです。もちろん、メーカー側もそれを理由に、以後の契約を再考することもありません。それが、当たり前の文化だからです。
契約文化にない日本の自動車メーカーは、欧州の部品メーカーに度々「塩対応」されて、問題解決に苦労する事が多いようです。価格や性能にメリットがあって契約しても、そこまで緻密な契約書を作る環境が無いために、相手の言いなりになってしまうのです。そのため、海外製部品が原因のリコールであっても、契約書の文面を突きつけられて、自社での対応を余儀なくされてしまうのです。
なぜか、同じ原因でリコールを繰り返す事例があります。その背景には、契約上の問題がネックになっている事例もあると聞きます。もちろん全てではありませんが、それを理由に国内回帰する事例も増えているようです。
次のページ>>1 2
スバルショップ三河安城 店舗案内

>>最新情報一覧
